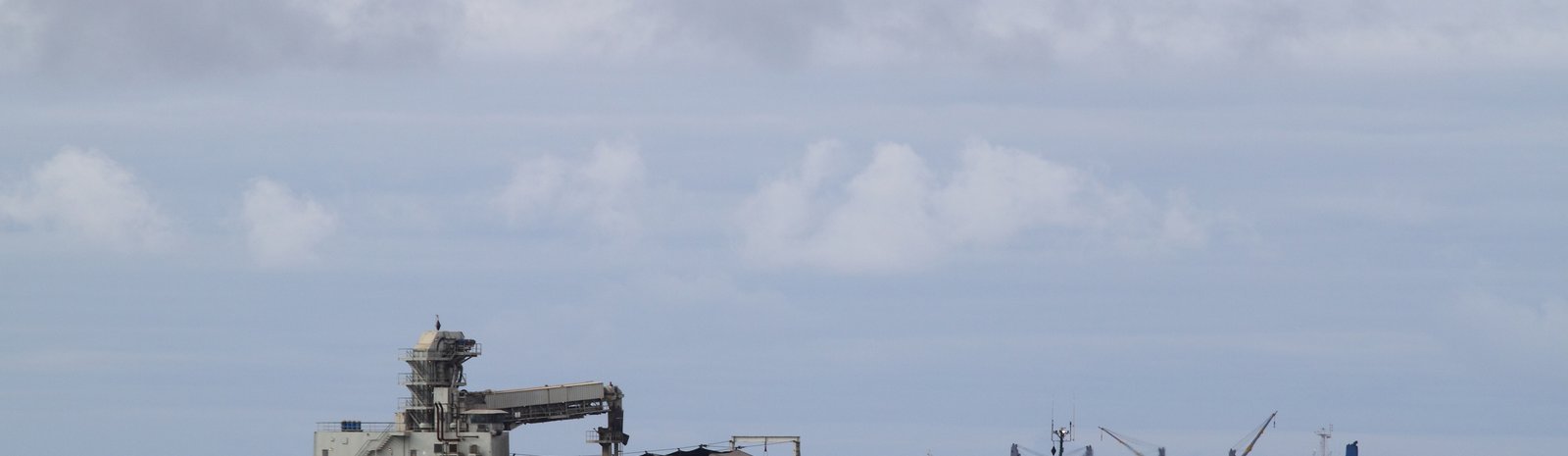
- Outline
- Summary
- History and Geology
- Mining Techniques and Waste Disposal
- Acid Mine Drainage
- Aqqaluk Project
- Employment and Revenue Sharing
- Environmental Concerns
- Running with Red Dog
- Latest News
Outline
- Summary
- History and Geology
- Mining Techniques and Waste Disposal
- Aqqaluk Project
- Employment and Revenue Sharing
- Environmental Concerns
- Latest News
Summary
The Red Dog Mine is a zinc and lead mine in northern Alaska, located about 80 miles north of Kotzebue in the Northwest Arctic Borough. This metal sulfide mine is the second-largest producer of zinc in the world, and is a major source of revenue for native corporations across the state. The main pit is almost out of ore, but in 2010 the mine began extracting ore from an adjacent pit, expected to last until 2031. The mine has had problems with wind-blown ore dust, and wastewater discharge issues have resulted in fines and a large lawsuit brought by the downstream community of Kivalina. Active water treatment and tailings repository maintenance will be needed forever -- to prevent heavy metals and acid discharge into downstream waters.
History and Geology
Metal deposits in the area around Red Dog Mine were first documented by USGS geologists in the 1950’s. These deposits are interpreted as precipitates from an ocean floor hydrothermal vent. These ocean sediments were then buried, metamorphosed, and finally uplifted by the same event that created the Brooks Range. Erosion of the Brooks Range exposed the resulting rock, which contains the worlds’ largest known zinc deposits, along with some lead and silver. Interest in mining these deposits was expressed by both the NANA Regional Corporation Inc. who owns the land, and by a mining company that later became the Teck mining corporation. In 1982 these corporations signed an agreement to develop the mine. In 1986 the State of Alaska agreed to construct a shallow-water port on the Chukchi Sea and a road connecting the port to the mine site. Construction on the port, road, and mine itself began in 1987 and the mine became operational in 1989. A large investment during 2009 led to a record amount of production that year, but the main deposit is expected to be depleted in the near future. The ore from Red Dog is shipped primarily to Asia where it is smelted and refined.
Mining Techniques and Waste Disposal
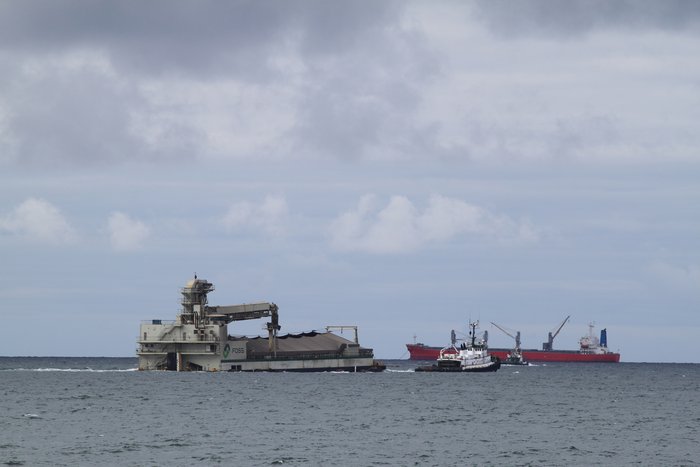
The Red Dog Mine is an open pit mine which is expected to ultimately reach 1600 m x 915 m x 122 m deep – more than 150 times the volume of the Empire State Building. Though this is a large operation, the ore at Red Dog is so rich that it is significantly smaller than other large mines that produce a similar amount of finished metal. The mine uses conventional mining techniques to extract an average of 9,800 tons of ore per day; first drilling and blasting the rock followed by grinding to a manageable size. The ore is pre-washed and then subjected to froth flotation which separates first the lead and then the zinc. This flotation process uses 200 tons of cyanide per year to increase the separation of the desired components. The resulting ore concentrates are dried using vacuum filters and then sent by road to the port where they are stockpiled until the 3-month shipping season in summer. The port doesn’t allow access to large ships so the ore is then ferried out by barges.
Acid Mine Drainage
_
…Acid mine drainage is a major problem with many hardrock mines, including almost all mines where the metal ore is bound up with sulfur (metal sulfide mines)…
…In particular, 90% of the studied mines that originally predicted “low acid mine” drainage potential had acid mine drainage problems at the time of the study…
…an additional problem can also be created when the acid reacts with rock that neutralizes it…
_
A critical facet of any metal sulfide mine is management of acid mine drainage. When sulfide-rich rock is exposed to the air, it can weather to form sulfuric acid. To prevent this at Red Dog, mine tailings are impounded with some of the waste rock underwater behind a large dam. However, most of the waste rock is stored in stockpiles on the surface, where acid is also generated. The acidic runoff from these piles is directed into the tailings pond, and then all water leaving the tailings pond is treated.
Since these sequestered tailings will leach acid whenever they are exposed, the impoundment will need to be maintained forever to protect downstream waters. The mine is expected to produce around 88 million tons of mine tailings if operation continues through 2031.
Power for the mine is produced by a series of diesel generators, totaling over 40 MW in capacity. Waste heat from these generators is used to heat the buildings on site. The mine uses 15.5 million gallons of fuel per year, plus another 1.4 million gallons for transportation and at the port. Some exploration and drilling for a nearby source of natural gas has been conducted but currently the entire mine is powered by shipped-in diesel. In early 2012, Red Dog announced they were terminating the search for nearby gas.
Aqqaluk Project
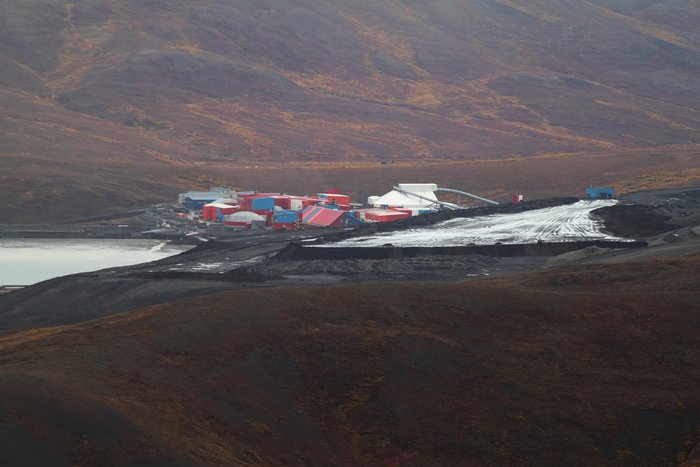
Because the main pit was projected to run out of ore in 2011-2012, Teck began mining of the adjacent Aqqaluk deposit in 2010. The permitting process to develop the Aqqaluk deposit was completed earlier in the year. Because this deposit was not considered in the initial Environmental Impact Statement for the mine, a new supplemental statement was conducted by state and federal authorities.
This Aqqaluk deposit has only 16% zinc, less than the main deposit at 20.5%, but is expected to keep the mine running until around 2031.
Most of the waste from this project will be placed back into the main pit of the original mine. However, the current tailing impoundment facilities will need to be modified for the additional waste, and the existing dams will have to be raised. After the deposit is mined out, the Aqqaluk pit will be filled with water to limit acid mine drainage.
Employment and Revenue Sharing
The mine employs around 475 people full-time and creates several dozen temporary jobs each year for a total payroll of around $50 million. The mine is the sole taxpayer in the Northwest Arctic Borough and in 2007 paid $230 million in state and federal taxes. Red Dog is also an important purchaser of goods and services in the region, and over half of the mine employees are NANA shareholders. The NANA corporation had set a goal of 100% shareholder employment at Red Dog but high turnover and jobs requiring extensive post-secondary education have kept this from becoming a reality.
Under Section 7(i) of the Alaska Native Claims Settlement Act, 70% of “qualified net profits” received by a regional native corporation from timber and mining operations must be divided among other native corporations in the state. This money is distributed to the other regional corporations, which then distribute half of it to the village corporations in their region. In 2008 NANA paid $122 million of Red Dog royalties to the other Native corporations. As a result, profits from Red Dog are a significant revenue source for native corporations across the state - forming the largest single contribution of income to many village corporations that are nowhere near the mine.
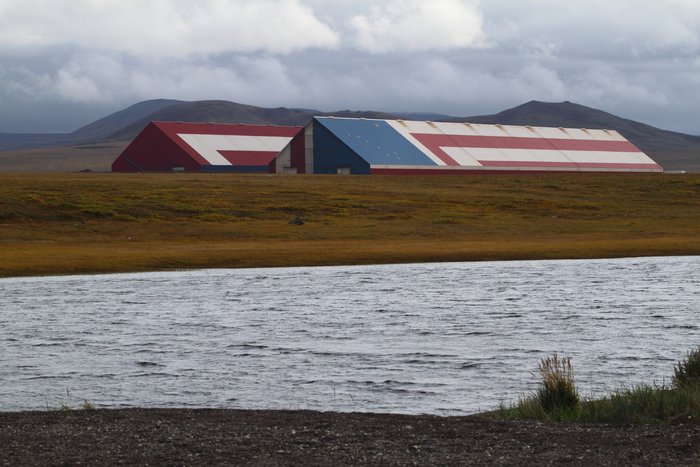
Environmental Concerns
The mine has had a number of problems with wind-blown ore dust, and with wastewater discharge issues. Active water treatment and tailings repository maintenance will be needed forever to prevent heavy metals and sulfuric acid discharge into downstream waters. In addition, there have been accusations that the road between the mine and the port is disrupting animal migrations and affecting subsistence living in the area. Lastly the existence of the Red Dog Mine infrastructure may be used as justification for additional mining projects in the area, such as the nearby Lik Deposit.
EPA Toxic Release Inventory
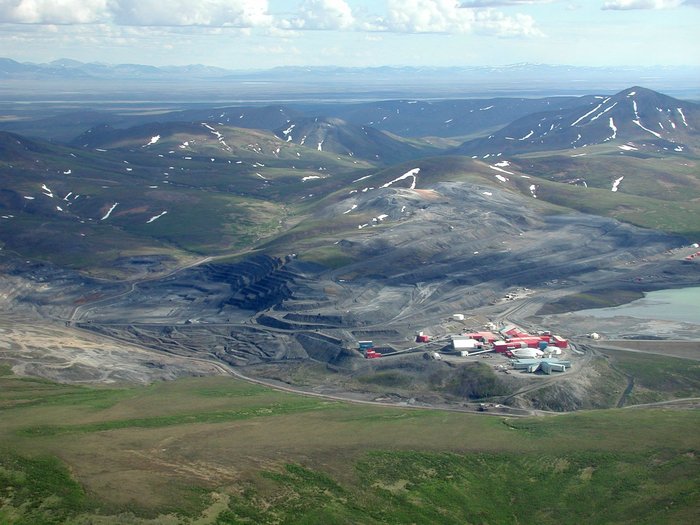
This aerial view, taken in 2000, shows the main Red Dog Mine mill complex. The mining pit is visible on the left and part of the tailings pond on the right.
 — 
<a class="figure-caption__link" href="/photos/red-dog-mine/">Get Photo</a></figcaption></figure>
Every year the EPA releases a list called the “Toxic Release Inventory ( TRI ),” which documents which industrial sites create waste that is considered to be toxic by the EPA. Red Dog Mine is by far the #1 site on the TRI, having produced 517 million pounds of waste material during 2008. This is primarily due to the high metal content of waste rock that is generated by this operation. Because these rocks contain zinc, lead, and other toxic metals they are reported as being released into the environment anytime they are moved or processed. Teck takes great pains to emphasize that this is not “pollution” but simply reflective of the minerals that were naturally present in the rock. However, fracturing the rock in blasting greatly increases its surface area, which leads to far more leaching of toxic compounds. Waste rock at Red Dog leaches acid and increases soluble metal levels, requiring water treatment.
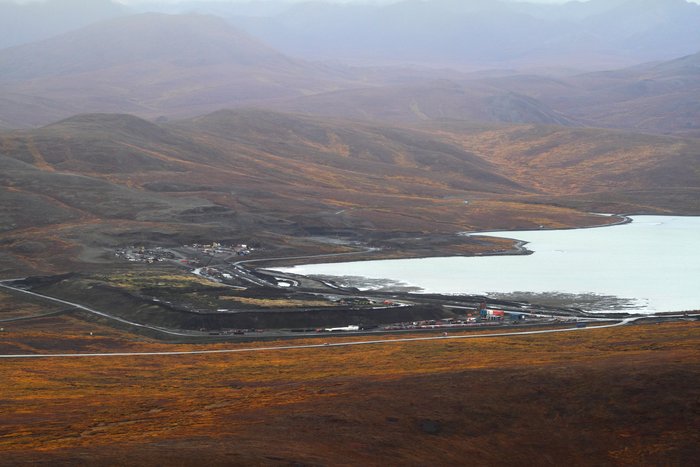
Water Treatment
To cope with the existing water flows in the area, the mine diverts Red Dog Creek through a series of ditches through the mine facility and releases the water downstream. Rain and snow on the waste rock and mine pit dissolves acid and heavy metals, which need to be removed before the water can be discharged. In addition, much of the water from the tailings pond is treated as well, both to be used by the mine itself and to maintain an appropriate level in the pond. Red Dog Mine uses lime and sodium sulfide precipitation to settle out the majority of the toxic metals in the wastewater before it is discharged downstream. However, the treated water is higher in “total dissolved solids ( TDS )” because the precipitation process increases the amount of calcium in the water. To maintain an appropriate level in the tailing pond, this water treatment will need to continue forever, at an estimated volume of around 1.35 billion gallons of water per year.
Running with Red Dog
_
.And what about tomorrow? Jim led me around the mine site, showing me all the complicated and careful procedures they use to treat the water before it is released, and how they make sure their discharge doesn ’t overwhelm the creek. He seemed proud of its complexity and thoroughness. But when the mine is gone, all of that must stay.
_
Teck emphasizes that the water downstream of the mine is now less polluted than before the mine began operation because EPA regulations allow less heavy metal discharge than were present in the natural rivers before mining began. They point to the recent establishment of a new population of protected arctic grayling downstream of the mine as evidence of the beneficial effect of the mine.
On the other hand, residents of Kivalina, a downstream village, are concerned about the TDS levels in their drinking water. In 2003 they brought a $60 million lawsuit against Teck claiming that Red Dog Mine had violated their discharge permits 2,600 times since 2002. The issue is complicated by the fact that Red Dog Mine has higher-than-normal “site-specific” TDS limits. An out-of-court settlement was reached in 2008 under which Teck would build a 53-mile pipeline, at the cost of tens of millions of dollars, to pump the wastewater into the Chukchi Sea instead. However, construction of this pipeline is still uncertain and not all the requisite permits have been obtained; in the meantime Teck has distributed reverse osmosis water purifiers in Kivalina. In 2009, Teck was also fined $120,000 for water-related violations at both the mine and port sites. These incidents included two spills, a time where heavy snowmelt overwhelmed the water treatment facility, and the dilution of wastewater with clean water upstream of a sample collection point. By 2014, little progress had been made on the pipeline and Teck was asking for extensions to their current higher-than-normal permit. By June 2014 Teck had apparently decided it was cheaper to pay the fines than build the pipeline.
Kivalina and others have also blamed the mine for fish kills downstream of the mine, but since fish kills also occurred before the construction of the mine it has been difficult to determine the exact causes. Since the mine now intercepts all the water coming from the deposit, they have de facto responsibility for preventing the kills even if they would have occurred in the absence of the mine.
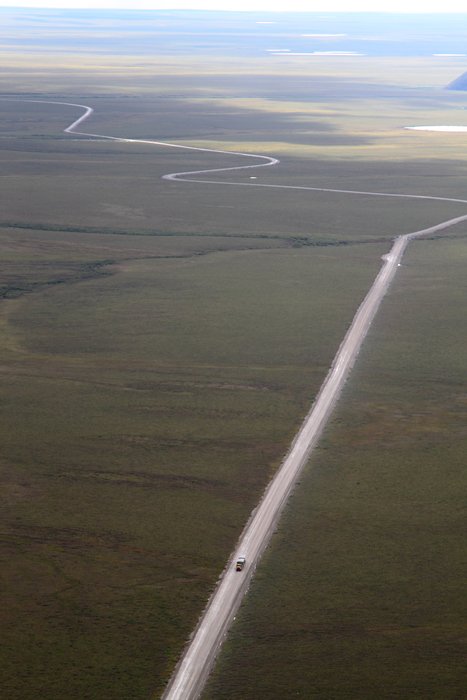
Fugitive Dust
“Fugitive dust”, or metal-laden dust that is released at the mine site or during transport, has been an ongoing issue at the mine. According to the EPA 2008 “Toxic Release Inventory ( TRI )” Red Dog Mine released 138 tons of fugitive dust in 2008. This dust is potentially toxic to a variety of plants and animals and contains compounds than can accumulate in the food chain. In 2001 the National Park Service released a study on the topic finding elevated levels of lead, zinc, and cadmium along the road. At this time both the mining corporation and the National Park Service began more detailed assessments of this problem. In 2007 a “final Risk Assessment for Fugitive Dust” was completed by a consultancy, concluding that in most cases the risks were relatively low, but that some measures needed to be taken. However, environmental groups have taken issue with the quality and conclusions of this second study. Teck has taken a number of preventative measures since the 2001 study; but the mine still releases large amounts of dust. In 2008 Teck released a “fugitive dust risk management plan” to again address this issue.
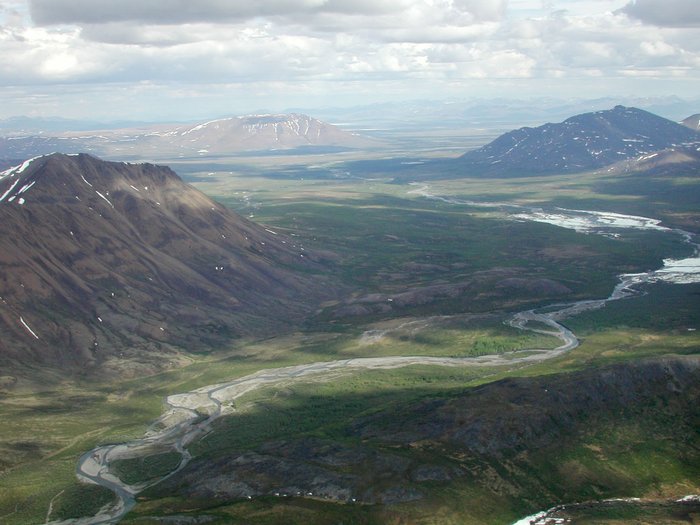
Reclamation plans
Metal sulfide mining reclamation is much more complicated than coal mine reclamation. In addition to re-contouring the landscape, Red Dog has to deal with tens of millions of tons of waste rock and mine tailings that need to be protected from air forever to prevent acid mine drainage. This means that the mine tailings pond needs to be maintained at an appropriate level in perpetuity, requiring regular inspections, maintenance, and treatment of over a billion gallons of discharged water every year. The treatment of the water is expected to produce almost 70,000 tons of sludge every year that will be buried in the mining pit for the next 50-100 years. In order to cover the costs of this reclamation project, Teck is currently required to purchase a “reclamation bond” worth over $300 million.
The ongoing water treatment and maintenance will require 7-15 full-time employees, 7,300 tons of lime annually, and retention of some of the mining equipment and infrastructure forever. The expected cost will be over $10 million per year.
In addition to the maintenance of the tailing pond, the reclamation plan for Red Dog Mine includes removal of the mining infrastructure, removal of creek diversions, re-contouring of some land, re-vegetation of waste rock stockpiles, surface and groundwater drainage control, erosion control, and ongoing site monitoring.
Latest News
A lawsuit was filed in February 2010 regarding a key discharge permit for the mine which could have resulted in a closure of the mine until this issue was resolved. In March 2010, Red Dog Mine recieved a new discharge permit from the Army Corps of Engineers, and in May Teck decided to proceed with development of the Aqqaluk deposit, although the final EPA discharge permits have still not been issued. In August 2012 a Federal court struck down a challenge to the discharge permits brought by the city of Kivalina. [m]: meters [MW]: megawatts
Further Reading
- > Red Dog Mine company site
- > Northern Alaska Environmental Center information on Red Dog Mine
- > A "virtual tour" of the Red Dog Mine created by the Alaska Industrial Development and Export Authority
- > Alaska Department of Environmental Conservation page on fugitive dust issues with Red Dog Mine
- > Wikipedia article on Red Dog Mine
- > Alaska DNR page on Red Dog Mine
- > NANA Regional Corporation Inc. website for Red Dog Mine
Created: Jan. 19, 2018