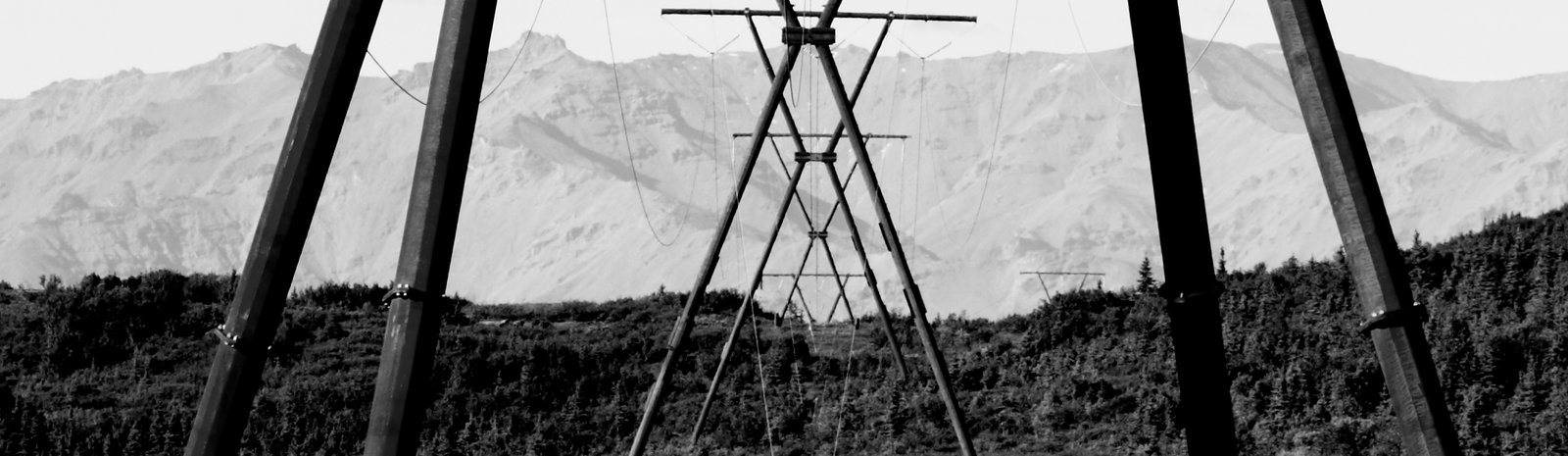
- Logistics
- Hazards and Impacts
- Electricity
- Electricity: Pebble vs. Alaska
- Diesel Fuel
- Diesel: Comparisons to Pebble (gallons)
- Why would the Pebble Mine use so much power?
- Hypothetical Carbon Dioxide Emissions from Pebble Mine
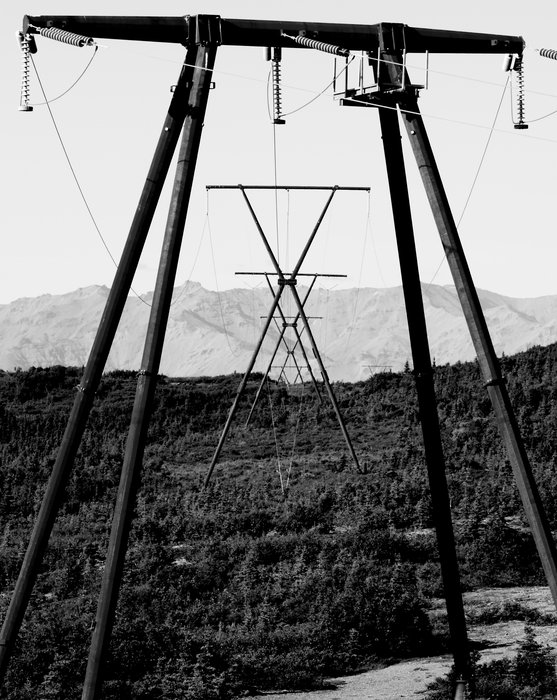
The proposed Pebble Mine would require about 400 MW of electricity generation capacity on-site and over 36 million gallons of diesel fuel annually. State diesel fuel consumption might increase by 6% or more as a result of a mine activities. 400 MW is almost 1/3 the amount produced by Alaska’s entire Railbelt electrical grid, which serves 500,000 people. Pebble’s powerplant would expand the state’s electricity production by 23%. This additional capacity would not be connected to the state’s electrical grids, but would serve the mine and the local area.
Natural gas, delivered by a pipeline from the mine’s proposed port on Cook Inlet, is the most probable fuel for electricity generation. Diesel fuel would be used for vehicle fuel and probably for other heavy, mobile equipment. Diesel would be delivered to the mine by a pipeline from the port. In addition to natural gas and diesel fuel, heavy fuel oil (also known as “bunker fuel” or “bunker C”) would be used by large ships bringing in supplies and equipment, and exporting ore. Jet fuel, currently used heavily by helicopters in the prospecting operation, might see continued use for mine-related helicopter and turboprop aviation, particularly personnel transport to and from the region. Gasoline-type fuels would probably be avoided for logistical purposes, with a preference for diesel equipment, and therefore see relatively little use on the ground. Finally, explosives would constitute a small but important fraction of the chemical fuels used by the mine.
Logistics
Powering Pebble is a major challenge. The Lake Iliamna and western Cook Inlet regions have no current energy infrastructure or fuel sources capable of servicing a large mine. There are no contiguous roads, water routes, or pipelines linking Pebble to either a reliable fuel source or to any other major infrastructure. The villages of Iliamna, Newhalen, and Nondalton, near the prospect, rely on the small Tazimina hydroelectric project, which has less than one megawatt of capacity, less than 1/300th of Pebble’s requirement. Oil and wood are used for heat. Fuel is currently transported to a small settlement on Cook Inlet, trucked overland on an unimproved road to the village of Pile Bay, and barged to local villages.
To resolve this challenge, Pebble Limited Partnership (PLP) has proposed building a 378 MW-capacity natural gas turbine plant at the mine site. As well as powering the mine, this facility could potentially provide low cost electricity to local communities, which are currently under financial stress from energy costs.
Hazards and Impacts
In the Lake Iliamna region, Pebble’s diesel pipeline may be the greatest environmental hazard in its energy-related activities. Leaks and ruptures could pollute local salmon streams. Storage tanks, both at the mine site and at the port on Cook Inlet, would be necessary to store diesel fuel, liquid natural gas, and possibly other fuels. Fluids used in small quantities, such as lubricants and hydraulic fluid, might be stored in portable drums. The rupture or damage of storage tanks or drums could lead to hazardous spills and fires.
In Cook Inlet, ship traffic and the resulting oil spill risks would present the greatest scale of hazard. Incoming ships carrying diesel fuel, natural gas, or other fuels could potentially spill their cargo accidentally, or wreck, releasing their cargo or their bunker fuel. The remoteness of the location would hinder rescue and spill response, and there are no major rescue or oil spill response resources on the western shore of Cook Inlet. However, it should also be noted that large shipping operations are generally conducted safely, and major accidents are infrequent. Smaller spills or accidents that arise from ordinary operations are much more common than major accidents, both on ships and in shore operations.
On a global scale, Pebble energy use would result in greenhouse gas emissions equivalent to more than 100,000 average Americans, or more than 400,000 average world citizens.
Electricity
Electricity is key to ore processing and camp operations at Pebble. Most notably, electricity would power the mill equipment which crushes and grinds ore into mud slurry. This activity is likely to be the single largest consumer of energy at the mine. PLP has proposed to generate this elecricity on-site, using a 378 MW gas turbine powerplant. Natural gas is currently the only serious option for electrifying the mine. PLP is considering three options for delivering natural gas to the proposed powerplant:
Electricity: Pebble vs. Alaska
Proposed Pebble Capacity: | 378 MW
Total Alaska Capacity: | 1750 MW
Permanent Jobs, Pebble: | 1000
State Population: | 720,000
KW/person, Pebble: | 378 KW/person
KW/Person, statewide: | 2.4 KW/person
1. Import liquefied natural gas (LNG) via ship to the mine’s proposed harbor on Cook Inlet, and then deliver it via pipeline to the the mine. This is currently the most likely option, using an established and feasible method of supplying natural gas.
2. Extract natural gas from Cook Inlet, and deliver it to shore via an underwater pipeline, then transport it to the mine via overland pipeline. This requires the discovery and exploitation of new reserves of natural gas under the inlet. Cook Inlet currently provides natural gas to southern Alaska, and the inlet’s gas is burned in Railbelt-connected generation plants, providing more than 50% of Alaska’s electricity. Although the Alaska Department of Natural Resources estimates Cook Inlet has far more natural gas is currently tapped, Cook Inlet faces an the impending gas shortage at present. Therefore, this option is speculative.
3. Build a spur pipeline from the proposed natural gas pipeline on the Kenai Peninsula. This option is contingent on the construction of the proposed pipeline, which may not ever be constructed.
Diesel Fuel
Conservatively, Pebble could consume over 36 million gallons of diesel fuel annually, and 3 billion gallons or more over a 78-year mine life. A dedicated diesel pipeline would continuously deliver fuel from the port to the mine site.
A 2007 Department of Energy (DOE) study concluded that diesel power is used for almost all material handling in the metal mining industry. According to the same study, roughly 17% of the energy consumed by U.S. mines comes from diesel fuel, and metals mining consumes, on average, 342,200 BTUs of energy per ton of material handled. PLP has not published a mine plan detailing exactly how much ore and waste rock it would extract, and in any case this would not be known until all mining was complete. Assuming 219,000 to 229,000 tons of material handled per day, 365 days/year, and 130,000 BTUs / gallon for diesel fuel, this yields 36 million gallons consumed/year.
This number is based upon Pebble Mine adhereing to industry average consumption, as identified by the DOE. Actual diesel use may be much higher, due to Pebble’s remote location, harsh environment, and the quantity of waste rock in Pebble’s low-quality ore.
Alaska’s Red Dog Mine may be a better analogue for Pebble’s physical situation. Although Red Dog ore is extremely rich compared to Pebble, both locations lack established infrastructure, including roads and electricity transmission. Both are reliant on ships and aircraft to transport ore, fuel, and equipment. Red Dog uses 15.5 million gallons of fuel per year directly, plus an additional 1.4 million gallons per year for transportation and at its port, to handle 9,800 tons of material per day - less than 1/20th of Pebble’s proposed daily volume. This fuel use rate includes all electricity generation (via diesel generators). If Pebble had equivalent energy requirements to Red Dog and satisfied 17% of that requirement with diesel fuel (as opposed to 100% at Red Dog), that would correspond to 64 - 67 million gallons per year, nearly twice our prior estimate.
Diesel: Comparisons to Pebble (gallons)
Exxon Valdez Oil Spill | 11-32 million
Annual Pebble Use, est. 1 | 36 million
Annual Pebble Use, est. 2 | 65 million
World’s Largest Oil Tanker | 92 million
Total Alaska Diesel Use, 2010 | 578 million
Daily U.S. Diesel Use, 2009 | 785 million
Lifetime Pebble Use (25 yrs), est. 1 | 894 million
Lifetime Pebble Use (25 yrs), est. 2 | 1,600 million
Alaska 2010 Oil Production, Diesel Component | 2,000 million
Lifetime (78 yr) Pebble Use, est 1 | 2,900 million
Lifetime (78 yr) Pebble Use, est 2 | 5,200 million
Est. 1: Estimated from Department of Energy 2007 U.S. metals mining figures.
Est. 2: Estimated from Red Dog mine fuel use.
Why would the Pebble Mine use so much power?
Hardrock mining is very energy-intensive, as it involves shattering, moving, crushing, and processing immense volumes of rock. Pebble may involve the excavation and transport of more than 23 billion tons of rock. For comparison, the Great Pyramid at Giza is estimated to weigh 6 to 6.5 million tons - less than 1/1,500th of the mass of rock to be excavated at Pebble. Hard rock mining is one of the most energy-intensive industries, requiring nearly twice as much energy to produce a dollar of Gross Domestic Product (GDP) as other manufacturing industries.
At Pebble, ore and waste rock broken loose from the solid rock body would be transported either out of a pit up to 4,000 feet deep (Pebble West), or from a depth of 5,000 feet or more underground (Pebble East). The ore would then be crushed and ground into mud. Crushing/grinding alone was estimated to consume 40% of all power used by U.S. mines in 2007.
Hypothetical Carbon Dioxide Emissions from Pebble Mine
Unit: Short Tons (2000 lbs.) of CO2
Total (Diesel + Natural Gas) | Annual CO2: | 1.9 million tons per year
Lifetime (25 years): | 47.5 million tons (lifetime)
Lifetime (78 year): | 149 million tons (lifetime)
Estimate is combined gtt-estimated diesel use & electricity generation. Other fuels & explosives are not included.
Natural Gas Consumption | Annual CO2: | 1.5 million tons per year
Lifetime (25 year): | 37.5 million tons (lifetime)
Lifetime (78 year): | 117 million tons (lifetime)
Assumptions: Powerplants typically vary in the amount of power (load) they generate, based on current demand. We assume the Pebble 378-MW plant runs 365 days per year, utilizing an average of 300 MW of its capacity, to account for variable load and down-time. This corresponds to 2,628,000 MWh of electricity produced, per year. CO2 output is 1,135 lbs/MWh.
Diesel Consumption | Annual CO2: | 400,000 tons per year
Lifetime (25 year): | 10 million tons (lifetime)
Lifetime (78 year): | 32 million tons (lifetime)
Assumptions: 219,000 tons of material is moved, per day, for a 25 year mine life. PLP’s projections rise, if the mine life is extended to 78 years, the maximum projected lifespan, to 229,000 tons/day. For our estimate, 36 million gallons of diesel/year is used, based on typical U.S. hardrock mine estimates. CO2 output is 22.2 lbs/gallon.
Lifecycle Emissions: construction activities, equipment fabrication, decommissioning & reclamation, and transport (aircraft and ships) to and from the mine site, of personnel, ore, fuel, and equipment, are not included in carbon output. Lifecycle carbon emissions are much higher than lifetime operating emissions. This table does not estimate lifecycle emissions.
Created: Jan. 19, 2018